4 real-life examples of digital twin technology
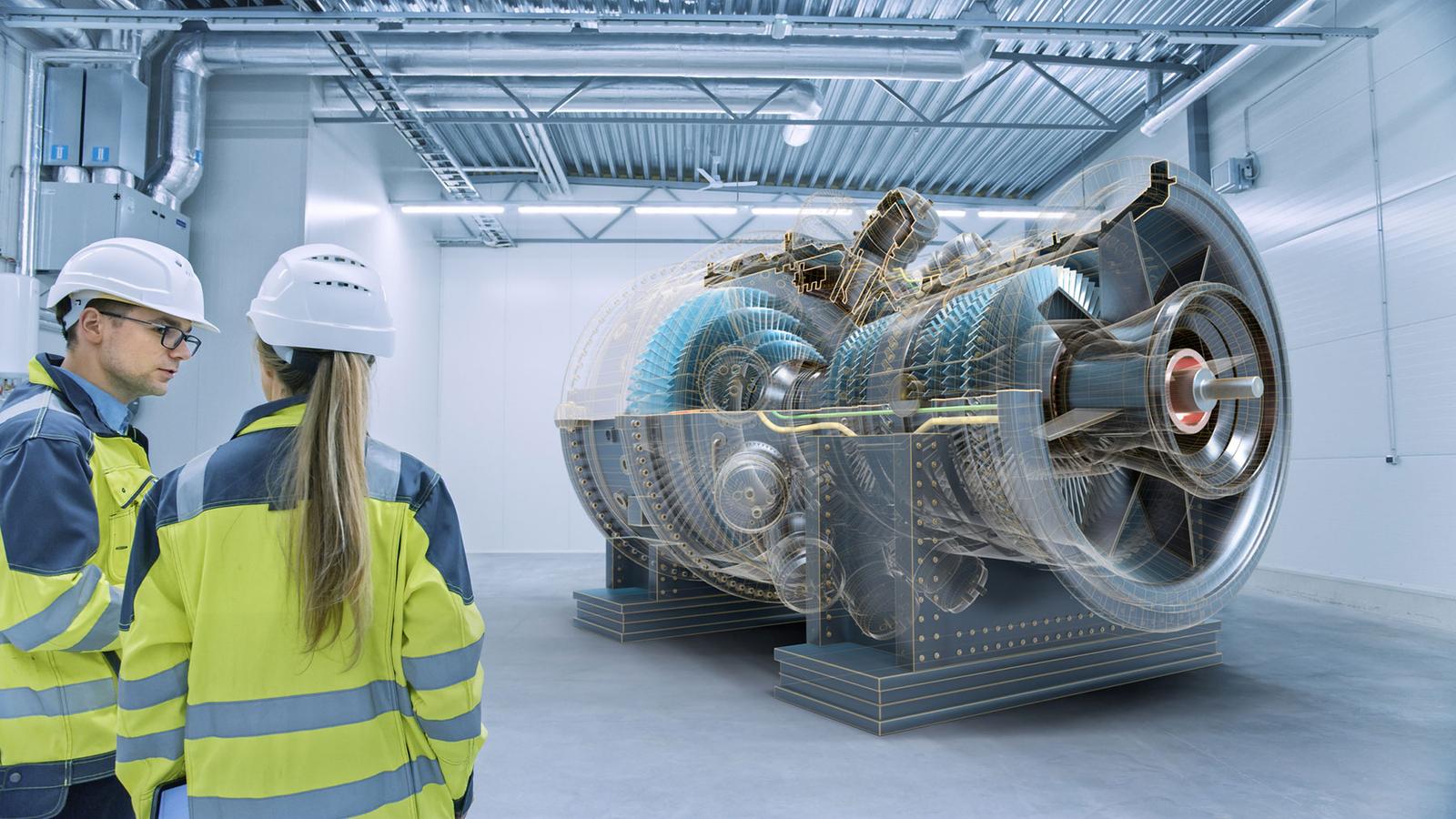
Digital twin technology is a virtual model designed to predict a real-life scenario accurately. Find out more here.
While a digital twin sounds like something akin to an avatar or virtual sidekick we’d want to have as our best friend in the metaverse, its applications are far more profound. Digital twins are taking off in a big way, and businesses are already using digital twin technology to develop new products, troubleshoot complicated processes, and proactively fix equipment before it grinds to a halt. According to Gartner, 13% of organizations implementing IoT projects already use digital twins, while 62% are either in the process of establishing digital twin use or plan to do so. If you haven’t come across the idea of digital twins before, you’re about to start hearing about it a lot more often.
Digital twins have been around as a concept in one form or another since the 1960s, back in the days when NASA was launching astronauts to the moon on hefty Saturn V rockets. Yet, they’re only now achieving escape velocity as a mainstream business technology — partly because the costs associated with them have recently dropped, and partly because IoT has ignited them with powerful analytics insights. But what exactly are digital twins, what can they do, and why would you want to have one at your company? Here are four real-life examples of digital twin technology that show the potential of these digital doppelgängers in action and illustrate why they have such a bright future.
Use these links below to jump to what you need:
- What is digital twin technology?
- What is the purpose of a digital twin?
- A brief history lesson on digital twin technology
- What are the different types of digital twins?
- The benefits of using digital twin technology
- Real-life examples of digital twin technology
What is digital twin technology?
A digital twin is an exact virtual replica of a physical object — anything from a car to an entire country — that organizations can use to better understand its current, future, and potential performance. Because a digital twin continually receives data from IoT sensors that have been placed on its real-world counterpart, it can give businesses in multiple industries precise insight into how their products respond to changing conditions in real-time.
What is the purpose of a digital twin?
Organizations can use digital twins to troubleshoot equipment that is far away or out of their reach — for example, a spacecraft flying beyond the boundaries of our planet. They can also use digital twin technology to design and test new products or scenarios, like a new car-braking system, to ensure they work as intended long before anyone begins using them. Digital twins are also perfect for understanding how products are already performing in the real world, in real-time, while customers are using them.
Digital twins offer companies valuable IoT-enabled insights on a regular basis, allowing them to refine their assumptions about how a certain product or process could work using predictive analytics. A business can even leverage a digital twin to understand how disparate systems interact with one another and accurately trace specific workflows or operations to highlight exactly where and how they could be improved. And with a visual view into complex systems-within-systems, engineers can more easily see how those interdependent systems behave and are linked with one another.
A brief history lesson on digital twin technology
NASA first pioneered the concept of a twin back in the 1960s. Engineers on Earth were unable to work directly with specific components of their spacecraft while they were in space. So, the agency decided to create precise replicas that the engineers could then use to simulate and study specific processes and functions from Houston. If you’ve seen the movie Apollo 13 or remember the Apollo era of human spaceflight, then you already know that this twinning capability became pivotal during that historic mission to the moon. An oxygen tank in the service module failed two days after launch and by running scenarios using an early twin at Mission Control, NASA was able to save the crew and bring them home.
This concept first went digital in the 1990s, when David Gelernter described it in his book Mirror Worlds. According to IBM, it was Dr. Michael Grieves who first applied the concept of digital twins to manufacturing in 2002. NASA’s John Vickers brought it full circle in 2010 when he coined the term “digital twin” as applied to digital simulations of space capsules and spacecraft. Gartner then named digital twins as one of the top 10 strategic technology trends in 2017.
Recommended reading: Top IoT trends for 2022
What are the different types of digital twins?
Digital twins can take many forms, from the smallest representation of a specific component to a macro-level view of an entire process or ecosystem. Here’s what you need to know about four of the most common types of digital twins: component twins, asset twins, unit twins, and process twins.
1) Component twins
Component twins are the simplest version of a digital twin, as they provide engineers with an example of a functioning component.
2) Asset twins
When two or more component twins are paired together to perform a function or process, they become asset twins. This type of digital twin allows you to study how these components interact with one another and continuously refine them as needed.
3) Unit twins
At the next level, we have unit twins — also known as system twins. This type of digital twin encompasses an entire functioning system of assets, so you can understand how they all function together and uncover ways to improve their performance.
4) Process twins
At the highest level, you find process twins. These digital twins portray how entire systems perform within a production facility and how interrelationships between their components can inhibit efficiency or diminish performance. Process twins allow an organization to optimize timing and orchestration for peak effectiveness.
The benefits of using digital twin technology
Digital twins offer organizations multiple benefits depending on the situation. They are ideal for risk assessment and mitigation, creating a virtual sandbox where companies can rapidly test a new process or idea without incurring substantial risks or costs along the way. Digital twin technology also accelerates production times and optimizes processes for greater efficiency, opening the door to cost savings. And with sophisticated analytics powered by IoT sensors, digital twins can also allow businesses to perform predictive maintenance on machines before they shut down and halt production, thereby cutting costs.
1) Optimized risk assessment and production times
Companies can use digital twins to test a product and make sure it performs as required well before it enters production — a key aspect of any good quality management process. Engineers can stress test the digital twin of their product, so to speak, subjecting it to a variety of scenarios to ensure it holds up as expected and then resolve any potential issues before they could impact customers.
This approach accelerates product development and whittles down production times. It also allows organizations to freely ask big “what if?” questions about their products and test hypotheses without the risks involved with running real-world simulations.
2) Predictive maintenance using IoT
Businesses can use digital twins to conduct predictive maintenance of products or pieces of equipment that are currently in production. By equipping the physical counterparts with IoT sensors and transmitting their performance data to their digital twins, organizations can pinpoint emerging issues before they result in downtime and even improve maintenance processes to better serve their customers.
3) Increased efficiency
By providing employees with better tools to do their work, digital twins can improve internal collaboration and boost organizational efficiency. With the digital twin providing up-to-date information on a products current state of health and the ability to automate specific processes, technicians have more time to focus on higher-level business priorities that deliver bottom-line growth.
4) Cutting costs
Organizations can use digital twins to cut costs, too. As Gartner reported, various industries — from oil and gas to supply chain — have used digital twins to reduce costs after COVID19 lockdowns. One of the main ways they can do this is through predictive maintenance. Digital twins can help companies identify equipment failures before they halt production, enabling timely repairs at a lower cost and even enabling automations that further reduce costs.
Recommended Reading: 6 Forward-Thinking Applications of IoT in Manufacturing
Real-life examples of digital twin technology
Digital twins are influencing the real world — from the individual human level of a personalized digital patient to a nationwide scale, in which an entire country can use them to prepare for climate change. Using this emerging technology, companies and organizations in the energy sector, hospitality, government, and healthcare are already finding creative ways to make our work and lives more efficient and meaningful. Here are four real-life examples of digital twin technology that are already in use today.
1) General Electric: Digital wind farm
General Electric (GE) leveraged digital twin software to create the first-ever digital wind farm. This allowed engineers to test up to 20 different turbine configurations to make sure they had landed on the best possible wind turbine design for the company’s real-world wind farm. The digital wind farm also allows site operators to collect and visually analyze site and unit-level data to maximize performance even further.
2) Carl’s Jr: Digital fast food
CKE Restaurant Holdings, Inc., the parent company of global fast-food chain Carl’s Jr, used digital twin technology to recreate hundreds of kitchen configurations to determine which one would achieve optimal productivity in its restaurants. The company went deep, mapping out every production process to simulate how it could be improved. They even threw new equipment into the mix to see what the effects would be before implementing any changes.
3) Singapore: Digital city
In one of the most ambitious applications of the digital twin concept to date, the city-state of Singapore created a virtual version of itself that includes building and transportation models of the entire country. Singapore’s digital twin is already helping one of the world’s top three smart cities identify strategies for adapting to climate change by addressing the rising sea levels that are a serious concern there.
The Southeast Asian country will also use digital twins to improve national water agency resource management and the rollout of renewable energy solutions. Ultimately, Singapore expects to create a core framework that orchestrates data sharing among multiple digital twins so the government can simulate different aspects of life there and run scenarios for different use cases.
4) Philips: Digital patient
Digital twin technology can even be used to create what Philips calls a digital patient — a digital twin of the human body — to help healthcare professionals provide more holistic, integrated, and personalized care throughout a patient’s lifetime. This digital patient will minimize risk to a patient during complex procedures, for example, a cardiac surgeon could fully simulate an operation before carrying it out on the patient in real life.
Digital twin technology is the future
Although a digital twin sounds like the avatar you’d choose for a video game or a virtual reality experience, it’s an increasingly mainstream technology that will profoundly shape the world (and beyond) in ways we’re just beginning to understand. It’s already helping energy companies make their wind turbines more efficient, allowing entire countries to plan for climate change, and even letting fast-food restaurants get that burger out to you just a little quicker.
According to Deloitte, IDC projects that by 2022, 40% of IoT platform vendors will integrate simulation platforms, systems, and capabilities to create digital twins, with 70% of manufacturers using the technology to conduct process simulations and scenario evaluations. If your company is already using IoT technology or thinking about doing so, you’ll want to keep close tabs on how digital twins will help your industry transform in the future.
Digital twins are only possible through the power of connectivity — connected sensors on the real life item are what make its' digital counterpart an accurate and useful representation. So, for digital twins to be beneficial, they first need to get connected. Hologram’s IoT SIM card offers seamless, global coverage for IoT devices with access to LTE/4G/3G/2G/CAT-M technologies. With our Hyper eUICC-enabled SIMs, you’ll gain access to new connectivity partnerships without any additional carrier negotiations, integrations, or hardware swaps.