Innovators of Things: How Ping Monitor turns wind turbines into IoT devices to detect damage
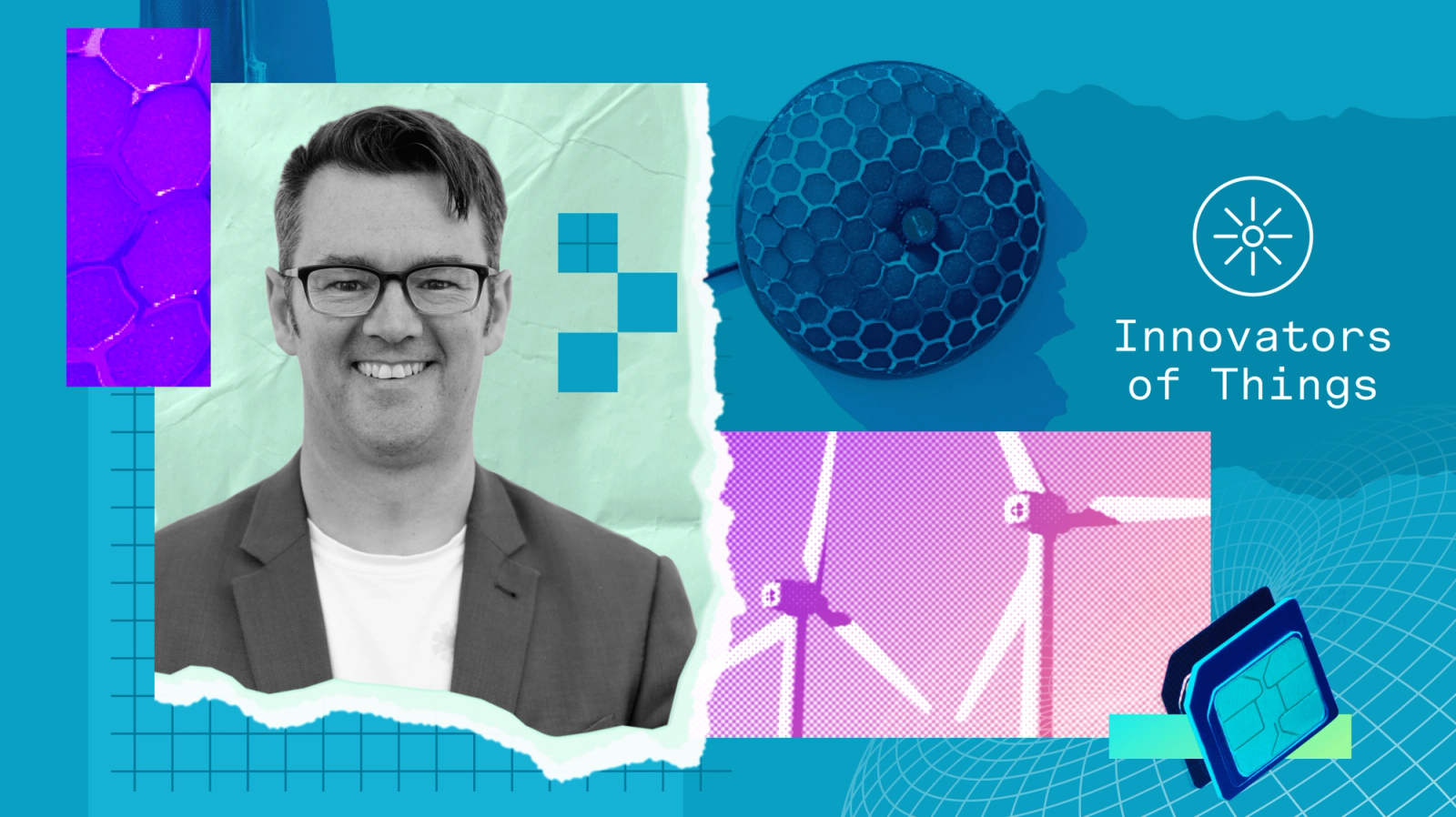
Leveraging cellular connectivity and sound to detect wind turbine damage to keep them operating.
Wind turbines are a huge source of clean energy around the world. In the US, it has the capacity to be the fourth largest source of electricity, with the potential to save hundreds of million metric tons of carbon emissions every year.
While these stats highlight the impact wind power can have on our environment, it’s critical that wind turbines continue to operate effectively. That’s where Ping Monitor comes in. Ping continuously monitors the health of wind turbine blades and uses advanced acoustic analysis to detect damage.
We spoke with Matthew Stead, CEO and co-founder of Ping Monitor, to learn more about Ping and the important role cellular connectivity plays in keeping wind turbines up and running.
Can you share more about Ping Monitor?
I have a background as an acoustician, specializing in sound. Several years ago, I learned from one wind farm operator that they could hear when there is damage to a blade. With my background in acoustics, I realized that it was possible to design a machine that could monitor the sound and quickly identify damage to a wind turbine blade.
Why is it important to detect damage?
Wind turbines are a high value asset but are often cost constrained. While they have the potential to generate power and save both on carbon emissions and energy costs, wind farms are also very concerned with reducing operating expenses.
The blades on a wind turbine are made from fiberglass, among other materials, and are exposed to many elements – rain, lightning, hail, dust, etc. While damage to a blade can often start small, the damage can grow over time, and what may have started as small damage can grow and cost millions of dollars or even complete structural collapse of a wind turbine.
How does Ping Monitor work?
Each device has a power and communications module and an intelligent listening sensor that magnetically attach to the wind turbine tower. The intelligent listening sensor continuously measures the sound from the wind turbine, which is recorded and analyzed directly on the device using edge computing. The results are then converted into a picture and sent every eight hours via cellular IoT, which is a critical component of the system.
The cellular connectivity allows our wind farm operators to access the data from the sensors and quickly diagnose any potential damage before they become catastrophic.
Why did you choose cellular connectivity?
Our devices needed to be easy for our customers to install and work wherever our customers are located. We support wind farms in over 17 countries today and wanted to ensure we had one provider who could serve all of our customers.
Hologram gives us the reliable, global connectivity we need at a cost that’s effective for our customers.
Can you share any examples of customers who have identified damage early and their savings?
We’ve seen customers save thousands of dollars not only on repairs but in looking at the ROI in reducing downtime. Ping has also helped lower inspection costs by partnering with drone operators. While Ping uses sound to detect damage, other companies offer remote monitoring through drones. In some cases, we partner with the drone operators where we will report damage, the drone can go inspect and diagnose the damage, and then send the team for repairs. Depending on the wind farm site, the financial savings are 3 to 6 times higher than the cost of our system. Ping has also saved potential complete blade failures which could have cost $300,000 to $600,000 to replace.
What’s next for Ping?
Ping has just released additional monitoring functionality (using the same hardware and IoT connectivity from Hologram) to monitor for lightning strikes, ice build-up and internal structural blade damage. We are now a more holistic wind turbine blade monitoring system, leveraging edge computing and cellular connectivity.